Maintenance managers in heavy-duty trucking fleets face a continuous battle against downtime, unexpected breakdowns, and escalating maintenance costs. One critical way to manage these challenges is to effectively prioritize vehicle fault codes. Here’s a guide on how to do it right, ensuring maximum uptime, safety, and cost-efficiency.
The Problem with Fault Codes Today
Every fleet manager is familiar with the overwhelming volume of data produced daily by vehicle sensors, diagnostic trouble codes (DTCs), and telematics systems. Without proper management, this flood of information quickly becomes noise—leading to ignored alerts and reactive, rather than proactive, maintenance strategies.
A common issue fleets face is reacting to all fault codes with equal urgency. However, not every fault code signals imminent downtime or severe problems. Knowing which faults demand immediate attention versus those that can safely wait is crucial for operational efficiency and cost control.
Prioritizing Fault Codes: An Actionable Strategy
Having the right tools – and specifically – a single place to view fault codes from mixed fleets and equipment is key. FleetHD has solved this problem by unifying data from any type of make, model, sensor and telematics vendor for a complete view of faults. Then, FleetHD’s advanced maintenance management platform uses a robust model for prioritizing fault codes. Leveraging AI-driven analytics and a configurable rules engine, FleetHD enables fleets to act strategically rather than reactively. Here’s how to make the most of your fault code prioritization:
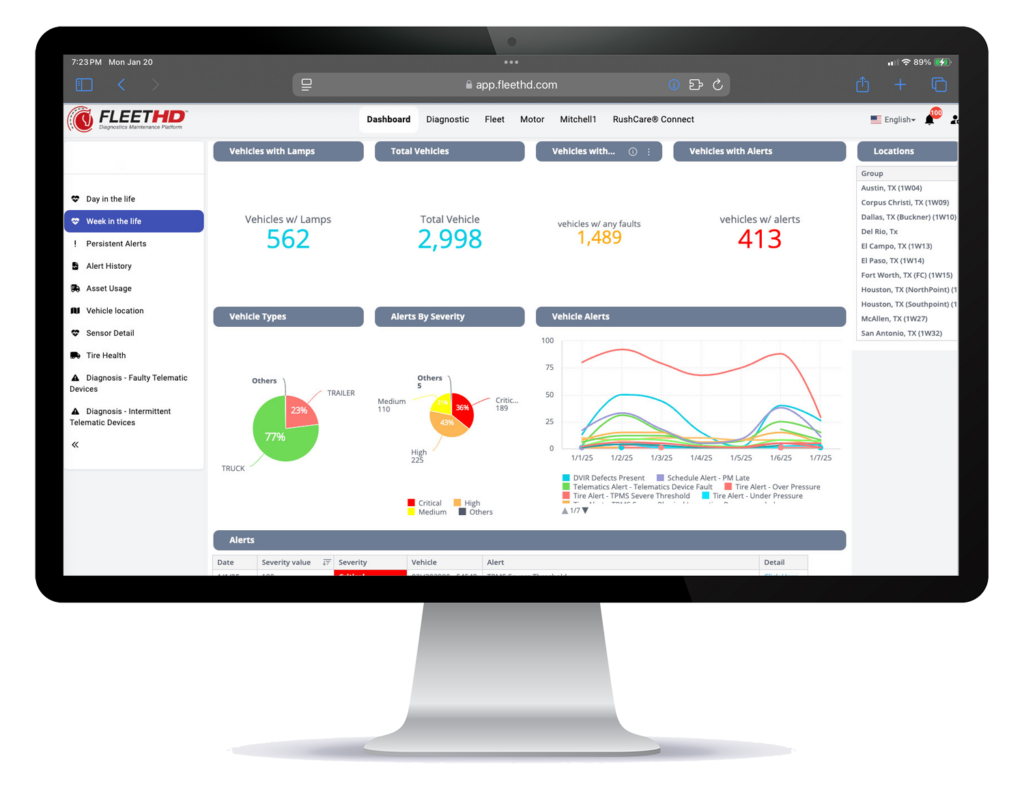
1. Filter by Severity and Urgency
Not all fault codes are created equal. FleetHD allows you to filter fault alerts based on severity, urgency, frequency, and even asset location. For instance, a coolant level alert may not initially be critical, but when coupled with rising engine temperatures or frequent recurrences, it escalates into an urgent issue requiring immediate attention.
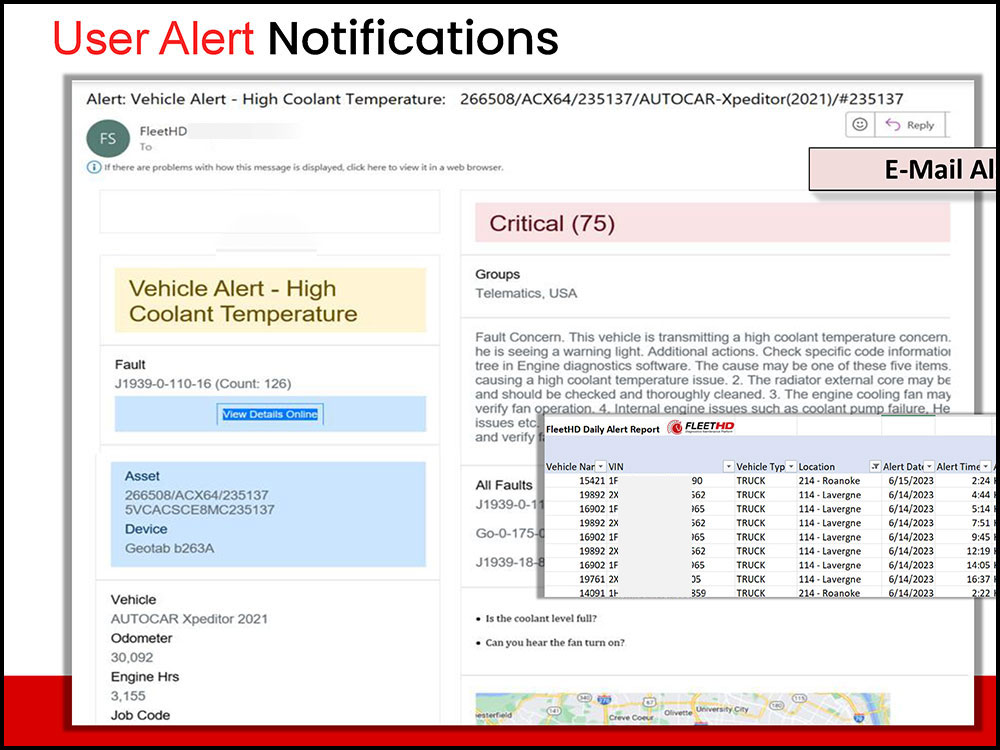
2. Implement Fault-to-Fix Intelligence
When a critical fault is identified, how it is handled is equally important. Using tools like FleetHD’s “fault-to-fix” intelligence provides detailed diagnostics, including:
- Exact fault description
- Step-by-step repair instructions
- Wiring diagrams and component locations
- VIN-specific parts matching
This ensures maintenance actions are precise and efficient, minimizing downtime and reducing unnecessary labor.
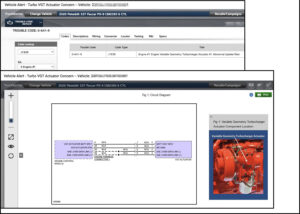
3. Proactive Maintenance Through Predictive Analytics
Moving beyond fault reaction, predictive maintenance can significantly minimize downtime. By aggregating data from ECMs, wireless sensors, DVIR reports, and telematics systems, FleetHD predicts when a component is likely to fail and suggests proactive repairs. This is also helpful to address other items on the vehicle that may need attention that could cause future issues. Managing the time in the shop is well-spent and can also minimize downtime. This approach transforms your fleet maintenance from reactive firefighting to proactive management, significantly reducing unscheduled downtime and maintenance expenses.
4. Prioritizing Alerts by Real-World Conditions
Effective prioritization also accounts for real-world operating conditions. FleetHD considers factors such as vehicle location and operating conditions to determine fault severity:
- Location-based alerts: An engine overheating in Florida requires a different urgency than the same condition in Minnesota in January.
- Vehicle-specific rules: Create tailored alert rules for different vehicle makes, models, and operational conditions.
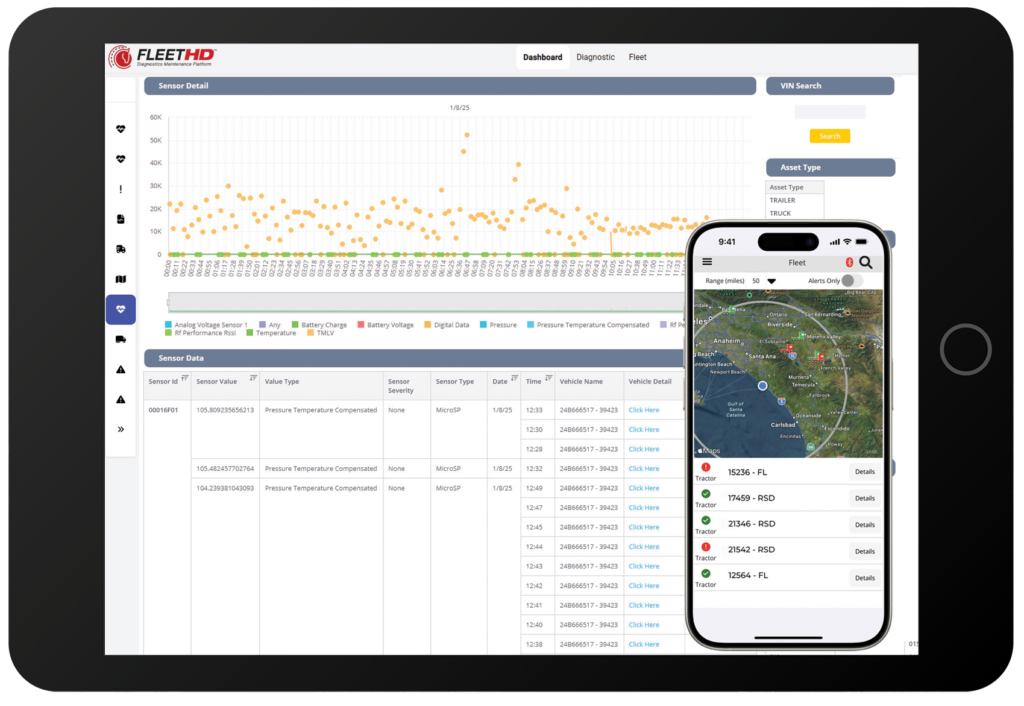
Measuring the Impact
Fleets using platforms like FleetHD have demonstrated significant improvements:
- Up to 13% reduction in maintenance costs
- 50% increase in mean time between failures (MTBF)
- Decreased emergency roadside assistance events
Fleet managers who implement these advanced prioritization strategies not only control costs but also enhance vehicle uptime and driver satisfaction, ultimately improving the bottom line.
Continuous Improvement Through Analytics
To ensure continuous improvement, FleetHD provides fleet-specific KPIs such as:
- Mean Time Between Faults (MTBF)
- Mean Time to Repair (MTTR)
- Fleet Health Percentage
By tracking these metrics, fleet managers can further refine their fault prioritization strategies, enhancing overall fleet efficiency and profitability.
Take Steps Now
The era of data overload doesn’t have to mean increased downtime or higher maintenance costs. With a structured approach, powered by intelligent data unification and predictive analytics, fleet maintenance managers can turn fault codes from operational headaches into strategic insights that drive real results.
Prioritize smarter, react faster, and keep your fleet moving forward with confidence. Embrace the power of predictive and prescriptive analytics—because when downtime decreases, profits rise.
Discover more about proactive maintenance with FleetHD and take control of your fleet’s future today.